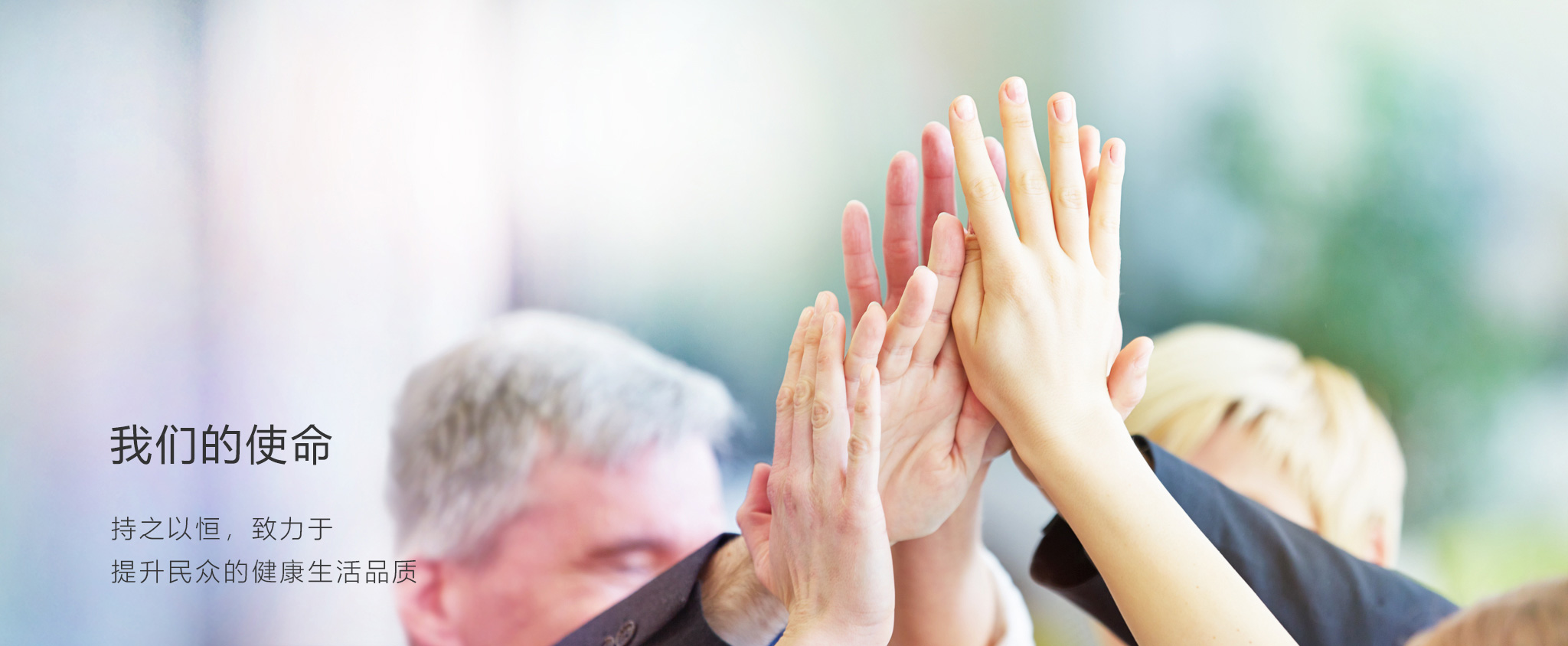
1、连铸坯缺陷的存在是决定于生产流程原料、 工艺、设备、控制、管理、检验等。
2、连铸坯表面存在裂纹,影响了铸坯热送率,从而导致了连铸滑坯现象。解决办法:改进连铸坯生产工艺,消除连铸坯表面裂纹。钢水成分硫含量偏高,虽然钢成分符合要求,但由于钢液凝固过程的选分结晶,凝固组织枝晶间的成分偏析非常严重,尤其是硫的偏析。
3、回答晚了点,方坯脱方,如果水质没问题主要是结晶器问题,水缝不均匀,或是铜管质量问题,精度达不到,造成初生坯壳薄厚不均,容易产生对角线裂纹,严重时会造成漏钢。
4、原因分析 1辊面热疲劳失效 热疲劳失效是造成连铸辊失效的主要原因之一。
1、连铸圆坯是指通过钢铁连铸技术,在连铸机上连续铸造出的圆形钢坯。目前,国家标准中对连铸圆坯的技术要求主要包括以下两个标准:GB/T 17426-2019《连铸钢坯尺寸、形状、重量和允许偏差》:该标准规定了连铸钢坯尺寸、形状、重量和允许偏差的技术要求,包括圆径、圆周、偏差、重量等方面的要求。
2、最为独特的是圆坯,其截面为圆形,根据直径的不同,分为管坯和锻造坯。直径小于300mm的圆坯主要用于无缝钢管的原料制造,而直径超过300mm的通常作为锻造坯,为各种锻造件的生产提供原料。特别地,不锈钢连铸坯因其独特的耐腐蚀性能,其应用范围更广泛,适用于需要高耐腐蚀性的行业和产品。
3、大圆坯连铸是一种连续铸造工艺,用于生产大直径圆坯的铜材料。该工艺通常在连铸机上进行,通过将熔化的铜液从底部注入铸模中,使其逐渐凝固并形成圆坯。铜是一种有广泛应用的金属材料,常见的铜合金包括黄铜、青铜和铝青铜等。
1、无缺陷连铸坯的生产技术 生产无缺陷的连铸坯是实现连铸坯热送热装的前提。否则,就不得不将连铸坯进行冷却,经过检查、处理后进入轧制工序,这样,根本谈不上“热送热装”。
2、连铸坯热送热装技术的实现还需要以下几个条件:(1)质量合格的连铸板坯;(2)工序间的协调稳定;(3)相关技术设备要求,如采用雾化冷却、在平面布置上尽可能缩短连铸到热轧之间的距离、通过在输送辊道上加设保温罩及在板坯库中设保温坑等;(4)采用计算机管理系统。
3、当采用热坯生产时,合格的连铸钢坯以单根方式从连铸热坯出坯台架送入输送辊道,输送辊道将坯料向前输送。坯料在输送辊道运输过程中经设在辊道中的坯料秤称重,自动显示纪录每根坯料的重量。
4、铸坯表面缺陷主要是指夹渣 、裂纹等。如表面缺陷严重,在热加工之前 必须进行精整,否则会影响金属收得率和成本。生产表面无缺陷铸坯是热 送热装的前提条件。铸坯表面缺陷形状各异,形成原因是复杂的。从总体上说,铸坯表面缺陷 主要受结晶器钢水凝固过程的控制。
5、铸坯剪切成定尺后,一般铸坯表面温度在800~900℃,约有540kj/kg的物理热放出来,为什么不利用铸坯的这部分物理热而要白白浪费呢?为此,从70年代人们就提出铸坯热送热装的工艺,也就是铸坯剪切成定尺后趁高温直接热送到轧钢厂装到加热炉内。
6、连铸简化了炼钢铸锭及轧钢开坯的工序,每吨钢可节约能量约(0.15~0.25)×10千卡。若进一步优化铸坯与成材轧机的配合,实现热送直接成材,能源节约潜力将进一步提升。连铸坯的结晶结构特点在于,钢水迅速而均匀冷却,形成较厚的微晶细粒表面凝固层,无足够时间形成柱状晶区。
连铸自动控制系统由生产管理级计算机、过程控制级计算机、设备控制计算机、各种自动检测仪表和液压装置等组成。
第三级是电气控制系统或仪表控制系统,是具体设备的执行者。它根据过程控制系统发送的设定值,精确控制设备的运行状态,执行具体的生产操作。这一层级确保了生产指令从高层传递到底层的无缝对接,实现精确控制。
生产过程中的计算机控制系统、电气传动控制系统、仪表控制系统三个自动化控制系统经常被总称为“三电”系绕。“三电”系统是现代大型冶金设备不可缺少的重要组成部分。 现代化连铸设备自动化的“三电”系统不仅占去设备总造价的相当比例,而且也是衡量连铸设备整体装备水平的重要标志,是顺利生产的重要保证。
连铸自动化铸坯跟踪和运行控制主要涉及铸坯的跟踪、存放地点记录、数量统计以及在铸坯上打印编号。这一过程通过铸坯跟踪和运行控制系统来实现,系统主要由钢坯探测器和微型计算机组成。各铸坯的堆放地点和原始数据均存入计算机中。
首先,规范的连铸流程能够显著提高生产效率。通过精确控制浇注速度、冷却速率和坯料拉出速度等关键参数,可以确保连铸过程的稳定性和连续性。这不仅有助于减少生产中断和故障,还能使生产线以更高的速度运行,从而提高整体产量。
首先是设备检查。在生产过程中,管道、水冷壳、水口、钢坯分机等设备必须定期检查,发现问题及时处理。设备运转稳定最关键的是维护保养,因此需设立严格的维护保养标准和计划,对设备进行定期检验和维修。其次是生产质量监控。连铸需要不间断的质量监控和检测。
规范设置连铸流程有助于确保产品质量。在连铸过程中,钢液的温度、流速、浇铸方式等都会直接影响到最终产品的质量。如果流程设置不当,可能会导致产品出现裂纹、夹杂、偏析等质量问题。因此,通过规范设置连铸流程,可以确保各个工艺参数得到严格控制,从而生产出高质量的产品。
通过规范设置连铸流程,可以最大限度地减少这些缺陷的产生,提高产品的机械性能和耐久性。例如,在钢铁连铸过程中,严格控制钢液的过热度、结晶器的振动频率和振幅,可以有效减少铸坯的内部和表面缺陷,提高钢材的整体质量。此外,规范的连铸流程还有助于提升生产安全。